[November 13, 2018]
Inside Hardware: Designing a New Component
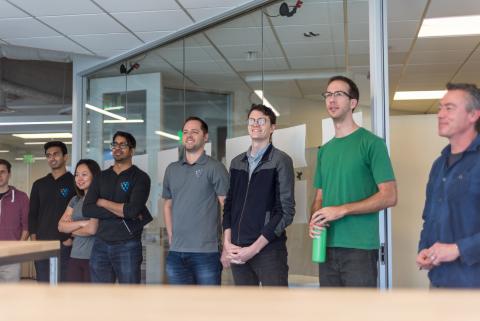
A conversation with Connor Kite, a Hardware Engineer at Shield AI.
How do you begin brainstorming the design of a new hardware component?
We start off with asking the question: What is the user experience that we want for this component? A lot of these are user-facing elements — latches, buttons, and any other things where you want a user to perform an action and it does something.
We discuss how the user will want to interact with the component: How can we make this easy and pleasing to use? That can constrain the design space in terms of what size package we have to work in and what kind of forces we can exert on things.
After that, we brainstorm a lot of different mechanisms and geometries until we get something that sticks.
How do you approach this process? What are the first steps after brainstorming?
I make some kind of simplified representation, frequently a model in a spreadsheet or a simulation, to gain an idea of the dynamics and kinematics we’d expect in the system. Because it’s easy when you are doing mechanical design to create something that looks good intuitively but then it binds up as soon as you start using it.
Inside a mechanism you may have two or three different components moving relative to each other, exerting forces on each other, and if you don’t do your due diligence, sometimes it could lead to a button you press and it doesn’t actually move. Even if the mechanism controlled by the button doesn’t seem to need that much force on it, the way you’ve created your mechanism could require a lot more force than you’d expect. So we typically create some kind of model simply to get an idea of what levers we can push on a mechanism design.
At the end of the day, you can do a ton of analysis, but prototyping is the key. So after the model, we fine tune the geometries in CAD and create our first pass prototype. This can be really simple and often doesn’t look anything like the final prototype. We’re really just trying to get a sense of how the mechanism works and pose questions like: How does this button feel when you are pressing it? How does this latch feel when it’s closing? Does it have a satisfying click or satisfying amount of resistance? From this, you may find your analysis does or does not capture everything. You get a baseline to tweak and refine so that after two to three iterations you end up with something you are happy with.
After all the iterations, you finish off with final cosmetic touches. At this point, if you are happy with the design and you have validated that it works as intended, you are ready to finish and move to production-ready processes.
How do you feel as a designer / engineer when you see the first prototype?
This is one of my favorite parts of the job. Prior to coming to Shield AI, I was more of a computation mechanical engineer. A lot of my work was simulation and there was not a lot of hands on design. The first time I got a prototype back at Shield AI was for a really simple battery latching mechanism. But getting that back and feeling the mechanism in my hands, and seeing that it actually worked was really exciting. That feeling of excitement when you get your first prototypes doesn’t go away. You either feel like “Yes, this works exactly as I thought it would!” or sometimes it’s “This isn’t quite what I thought but I can see the path to get there.” Either way, the first prototype is where you learn the most about how to build the final product.
How do you see the role of trust in hardware and design?
That is really important — on the mechanical side, when you are designing the hardware it needs to be something that feels like you can trust it. It needs to feel sturdy and you need to believe it will work every time just as you would expect it to work. Part of that is designing for robustness so things don’t break unexpectedly, but it’s also getting the feel right. This goes back to my example of the button; if a button is super light and you can press it too easily, it can feel cheap. So part of our work is getting the feel right so things feel luxurious and well put-together. There’s a craftsmanship to it.
How do you think about craftsmanship?
There is craftsmanship in design. You can do a more thorough or less thorough job. You can get into the nitty gritty details of how these components look and feel and how will they make people feel. Ultimately, I think that is what separates something that you just use and it’s okay to something that you really want to use. That is what we want our customers to feel and experience.
Have you had experiences where you get to see customers interact with your product? What were those like?
We are very lucky to be able to work closely with our customers and we receive feedback from them often. One interesting experience I had was designing the case that Nova goes into. This is probably technically one of the least exciting things we do, because it’s just a box with foam. But I did spend a lot of time thinking about how everything would be arranged and how the user would interact with everything that goes into that case. When we had one of our customers come in to see it, there was just so much excitement and this feeling that this was a product and this case brought everything in it together. It was a premium experience.
What factors did you consider when putting this case together?
One would be cosmetic: Does it look balanced?
Another aspect would be smaller details, such as the pouch where paperwork goes. I spent a lot of time just mocking up pieces of paper and considering how it feels. Does anything bind up?
The slots for the batteries — is it easy to get them out, but not too easy?
Even how we ensconce the phone in the case — we have it on an insert but it’s flush with the surface of the foam so it almost looks like what you would get in a consumer experience when you open a package; it’s very clean cut.
What do you want customers to feel when they interact with the products you design?
First of all, it is trust — just a deep-seeded feeling that they can rely upon this. People are going to be relying on this product and there should not be any feeling of doubt. A lot of that is the software capabilities but hardware communicates a lot in terms of quality to the customer.
How does hardware communicate to the customer?
Even if our software worked flawlessly, but the package that Nova came in looked insufficient, it would not be something that inspires trust. I believe you ask yourself — at least on a subconscious level — if these details weren’t taken care of, what else wasn’t taken care of? A lot of times when I am doing design, sometimes you just know when you are done with something because it reaches a point that it looks like a real product. Typically when something looks and feels like a product it’s because there’s a subconscious feeling that it looks like it’s going to work and that it will work well. There are a lot of subconscious cues people pick up on by looking at the product.
How do you think about design in a very high stakes environment?
In our design we are really trying to push the limits of what we can achieve in terms of flight time, cutting down weight, finding as much performance as we can, which means not over-engineering everything. But for a high-stakes environment, you need to verify and extensively test that the design decisions you are making will not lead to reliability issues down the road and affirm that this product is something that can be trusted.
How much does reliability play into decisions you make?
Significantly — when we are making designs, even if it’s just how you size something or how you choose one mechanism over another for the same job, a very important question to ask yourself is which of these will be more reliable?
Are there books or influences you come back to?
I would say that The Design of Everyday Things by Don Norman is a great one. It introduces a lot of important concepts about design that I work to hold on to. You can boil down those concepts to the idea of really having the customer or user in the forefront of your mind at all times and really walking through how they will interact with the product, how will they want to interact with it, how do they need to interact with it? And always use those questions as your guiding point.