[December 11, 2018]
Inside Hardware: Visiting a Manufacturer
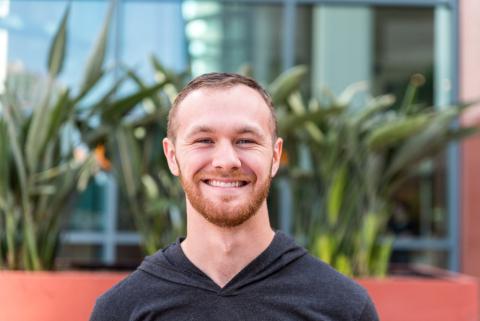
A conversation with Mitch White, a Hardware Engineer at Shield AI.
You were the lead on designing the battery charger that comes with Nova. Where did you start with this design?
At Shield AI we’re fortunate enough to maintain ongoing open dialogues with our customers and to have colleagues who have been in our customers shoes. The hardware engineering team was able to visit our customers’ operating base and see the area where they stage and store all of the electronics they use. This helped me to formulate ideas of how I wanted the battery charger to operate. Even though the charger is an accessory to our core product, I didn’t want it to be designed as an afterthought — I wanted the experience to be seamless.
How did your visit to the customer inform your product design?
They have the need for so many electronics, cables and power adapters. It inspired us to build something really compact so as not to add to the clutter.
The specific takeaways that informed the charger design were:
- We needed to minimize our floor space. Rather than design a huge power brick akin to a laptop charger, we wanted to integrate the charger so that it was just one box with a cord that goes into the wall. This keeps it really simple, and more importantly, it minimizes the number of things our users need to keep track of to operate the charger.
- We needed a product with better-than-average durability. Our product needed to withstand wear-and-tear; it couldn’t be flimsy. So we knew that we needed to look beyond consumer-grade products for inspiration. Understanding the environment our product would be used in informed durability metrics for us.
What happens after that?
Once we understood the customer’s environment, we started to think about how we wanted someone to interact with the product. Since we were competing for floor space, one priority was to have the battery insert from the top instead of the front or side. Minimizing the footprint and using the space above the charger for battery insertion and removal were priorities based on our observations.
Another carefully thought-out detail was how many bays to put into the charger. We could have done just one charger per battery, but integrating 6 into 1 gave the customer more efficiency and flexibility.
From there, the design process transitions to 3D printing parts. This stage allows us to prove that we have something that will work. This stage is also where we can flesh out some key challenges. For example, early on we discovered the charger was unbalanced. All the batteries were pulled upward from the front, but there is a huge power supply in the back, so it had a tendency to tilt backward. We added weight to the front to prevent this tilting. Using 3D printing early allows us to look closer at the user experience.
What is the role of 3D printing as you think about design?
It’s extremely versatile and only getting better. A large part of the mechanical design process occurs on a computer screen in 3D modeling software, but there’s nothing like being able to hold a prototype in your hand. 3D printing gets prototypes into our hands faster and at a lower cost than conventional methods. This has become crucial to the design process. With regard to engineering prototypes, we’re mostly examining form, fit, and function.
Form is the general aesthetic of a product. The ability to judge form is something universal that is not unique to mechanical design. Everyone has a gut feeling when it comes to aesthetics, so it is important to get this right. It is very easy to design things that don’t look like a product.
Fit looks at the ability to assemble the product. With more than 40 unique components in the charger, there can easily be unforeseen complications during the assembly process. 3D printing is typically an effective stand-in for injection-molded plastics, although it is necessary to understand the limitations of 3D printing where part tolerances or material performance are critical.
Function is validating that a mechanical design performs as it should, and validating that the design meets environmental requirements. This includes everything from drop-testing, thermal design, rain, dust, and any other variables presented by the anticipated use case. 3D printing gets us 90% of the way toward validating a design on this front. The one major limitation is in drop-testing. 3D printed materials will not perform the same way as the final material, so additional due diligence is required here.
After you create the design and see it 3D printed, what do you do?
We take a number of steps to validate the design. We do environmental testing to check for things such as thermal performance. The internal components and batteries generate heat and the testing process informed us that we needed to add fans to the assembly. We worked closely with our electrical engineers to integrate a fan into the existing architecture, to measure the temperature inside the case, and to complete the testing needed to ensure we will be able to operate in an environment representative of our customers’ operating conditions.
What is the next step?
Once there is confidence in the design, we begin the process of producing parts. In the case of the battery charger, Shield AI engaged with a contract manufacturer in order to produce the charger at scale. Eventually, we will schedule a visit to the manufacturer, but before that visit, we have them send us samples. We examine these samples and take the necessary steps to build the product ourselves and to make sure all works just as expected during assembly.
The actual visit to the contract manufacturer for a product validation test (PVT) is a way to confirm the transference of all of the assembly requirements and quality controls. We need to be able to see the parts together and to discuss the product in person. Critical to this process is a thorough and patient operations team to help bridge the gap between the mechanical design and the contract manufacturer’s end product.
How did you feel as an engineer seeing the evolution from task to product?
The work required to move a design from something that lives in 3D modeling software to something we built in-house to a mass-manufactured process was not only extremely difficult, but extremely rewarding. This is a team project, and when the team sees the finished product we designed — it’s an indescribable feeling.