[August 19, 2019]
Inside Hardware: Designing a Circuit Board
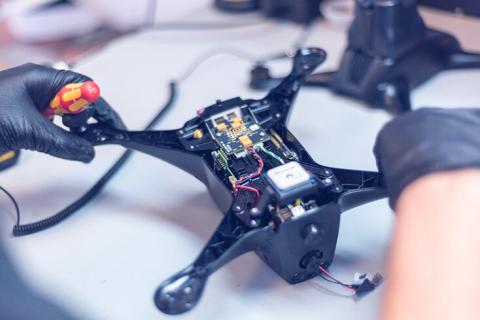
Why are circuit boards important?
At the simplest level, circuit boards are the glue that integrates all of the higher-level system features together.
Where do you start when designing a circuit board?
There is a lot that goes into circuit boards — power regulation, filtering, different communications, buses, and chips — but before you get down to the level of picking components, you may not have a clear indication of exactly how each component will be connected. You don’t know what’s on the board, you just know what needs to come in and what has to go out. You start with the architecture and figure out implementation specifics later.
At Shield AI, when we are designing circuit boards for Nova, we begin by identifying the functional requirements, the customer needs and the customer pain points. From there, we determine what sensors and other items should be included in the design to meet those needs. We choose the key features first and then work from the outside in — things like cameras, illumination systems, imagine processing, compute, battery power, and propulsion need to be selected.
Once you’ve chosen the technologies to include in the product, then you ask, “How do we connect these?” And that’s where the circuit boards start to come in. Then it becomes a matter of connections and tradeoffs: We have a motor, so we need something to drive it, but we also need to prevent the circuit from overheating. You just keep working your way back and balancing tradeoffs.
At Shield AI, what makes circuit boards particularly challenging to design?
Circuit boards and connections generally are more complicated than one might imagine. But, what makes them particularly challenging at Shield AI is our size and weight constraints. Since Nova is an aerial robot, we’re always focused on weight because extra weight means a reduction in the robot’s flight time. Similarly, we always seek to minimize space because Nova must be small enough to navigate narrow doorways and tiny gaps, and to fit in a backpack.
When things start to get that small, the design becomes more complicated, but that’s when it also gets more interesting. For instance, we work with many fast edge rate digital signals but, due to the compact size of the robot, we do not have the space required to include a shield or to increase PCB thickness with added GND layers. This means we have to devise alternate solutions.
How do you approach solving that challenge given the size and weight constraints?
For solving potential EMI and coexistence issues, we evaluate the performance of different matching networks in simulation, evaluate benefits of advanced PCB fabrication approaches, or adjust sensor locations and cable placement to reduce coupled noise.
We design in a space where typical rules of thumb aren’t sufficient to fully characterize or optimize our systems. The size, weight, and signal integrity constraints require that we deal with these challenges by being very strategic in how we architect the system from square one. We have to get down to the bare fundamentals where most engineers don’t typically spend a lot of time. We have to really understand problems at their most basic level to model, measure, and overcome them.
What is the relationship between the mechanical engineering team and electrical engineering team in designing a circuit board?
In most organizations developing hardware, there is contention between the mechanical teams that want to keep things small and the electrical teams that want more space. Here, we have a mutual goal to keep things as small as possible.
The electrical team accepts that it makes our designs harder, but if we design the smallest circuit board possible, it helps our customer. If it’s smaller and lighter, the quad will have more flight time and that’s better for everyone. So when you have a mutual goal, the give-and-take is seamless.
Having a mutual goal means that the mechanical team knows that it can trust that the electrical team is trying to design boards to be as small and efficient as possible. So when we go to them and say we need more space, there’s not a battle over how much more we need. We just look at the CAD together, as a team, and figure out what it will take to facilitate our design.
And that is unique. I’ve never met a team anywhere that has that kind of relationship. I often find that, in trying to describe this dynamic to people outside of this organization, it seems a little too good to be true because it’s just so uncommon. But, in order to best serve our customers, we work side-by-side here.